航空發(fā)動(dòng)機(jī)壓氣機(jī)轉(zhuǎn)子葉片工作溫度高、受力工況復(fù)雜、服役環(huán)境惡劣,工作時(shí)主要受離心力、氣動(dòng)力、熱應(yīng)力、交變力等多種負(fù)荷,對(duì)材料的疲勞性能要求較高。此類(lèi)葉片往往型面復(fù)雜,具有較大的曲率半徑和扭轉(zhuǎn)角度,是典型的復(fù)雜薄壁異形零件[1-2],對(duì)成形尺寸精度要求高,生產(chǎn)工藝路線長(zhǎng),制造難度大[3]。航空發(fā)動(dòng)機(jī)壓氣機(jī)葉片的制備技術(shù)先后經(jīng)歷了純機(jī)加工、普通模鍛、半精鍛到精鍛的發(fā)展歷程[4]。
精鍛技術(shù)是在普通模鍛技術(shù)的基礎(chǔ)上發(fā)展起來(lái)的一種精密成形技術(shù),可使葉身精確成形[5],葉身型面和緣板內(nèi)側(cè)無(wú)須加工,這在很大程度上減少了機(jī)械加工量[6],該技術(shù)被喻為“綠色制造”。經(jīng)統(tǒng)計(jì),全球采用該方法生產(chǎn)的航空發(fā)動(dòng)機(jī)葉片已占到生產(chǎn)總量的80%左右[7-8]。經(jīng)過(guò)精鍛成形后,葉片尺寸精度高、內(nèi)部組織均勻,其抗疲勞性及使用壽命顯著提高[9],因此,精鍛技術(shù)已成為航空發(fā)動(dòng)機(jī)葉片制造的主流工藝。
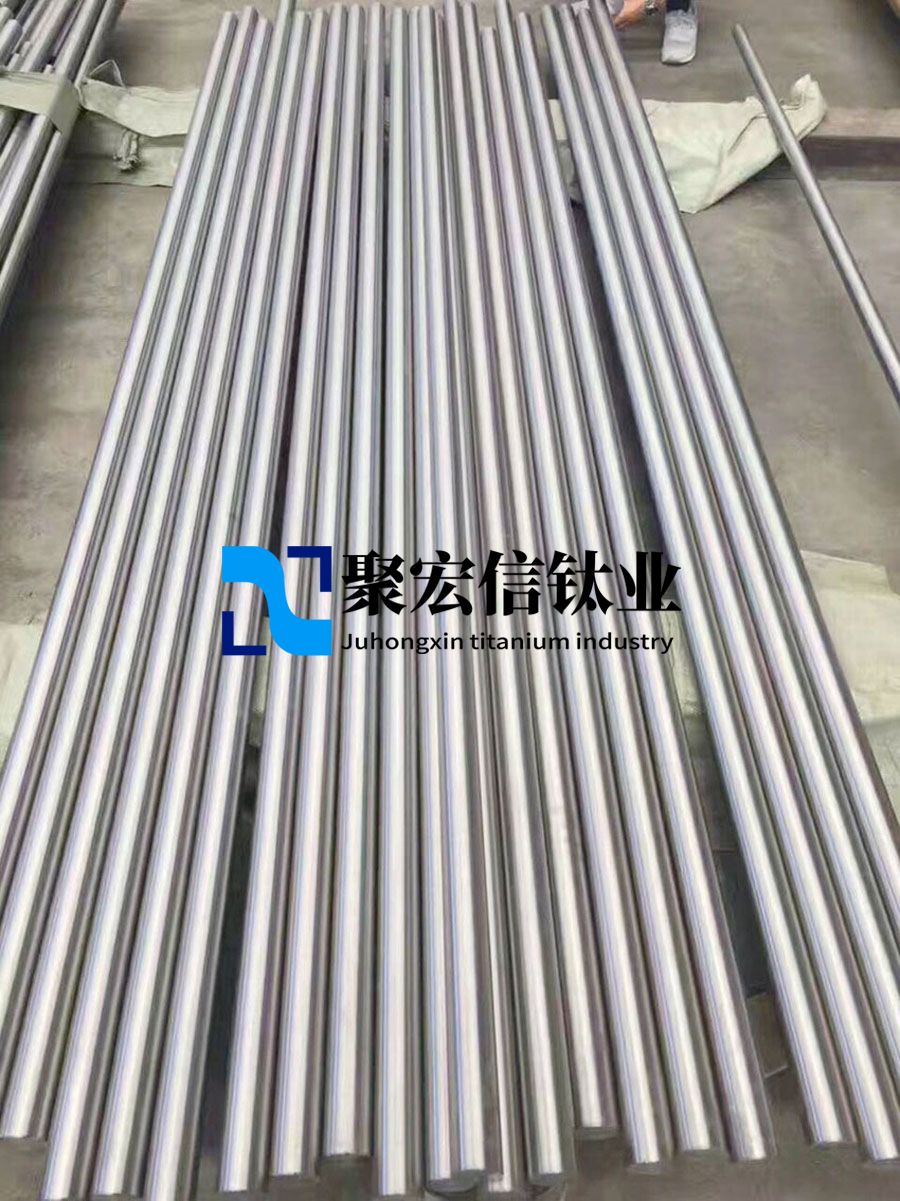
航空發(fā)動(dòng)機(jī)葉片材料的發(fā)展趨勢(shì)是高性能化(如輕質(zhì)、高強(qiáng)、高模、抗氧化等)和低成本化[10]。先進(jìn)航空發(fā)動(dòng)機(jī)技術(shù)的進(jìn)步推動(dòng)了高溫合金的快速發(fā)展[11],高溫合金具有較好的熱強(qiáng)性、抗腐蝕性和長(zhǎng)時(shí)組織穩(wěn)定性[12],已成為航空發(fā)動(dòng)機(jī)壓氣機(jī)葉片的主要選材[13-15]。GH4169是目前航空發(fā)動(dòng)機(jī)上用量最大的變形高溫合金,它主要由δ相、γ″相、γ′相及碳化物強(qiáng)化而成[16],具有良好的高溫強(qiáng)度、耐蝕性能、熱加工性能及焊接性能,被廣泛用于制備變形渦輪盤(pán)、軸、環(huán)、機(jī)匣、葉片及緊固件等零件[17-18]。目前,有關(guān)GH4169合金用于制備盤(pán)軸類(lèi)大型鍛件的研究較多,主要集中在鍛造溫度、應(yīng)變速率、熱處理以及析出相分析等方面[19-20]。隨著航空發(fā)動(dòng)機(jī)推力的增大,對(duì)葉片的性能要求也逐漸提高,要求葉片鍛件流線不能外露,普通模鍛技術(shù)難以滿(mǎn)足該要求,從而助推了葉片精鍛技術(shù)的發(fā)展[21]。葉片精鍛成形工藝可保持金屬流線連續(xù),增加了葉片的強(qiáng)度和承載能力、提高了葉片的性能,同時(shí)由于加工量少,從而節(jié)約了材料,解決了復(fù)雜薄型葉片難加工的困難[22]。本文主要以航空發(fā)動(dòng)機(jī)高壓壓氣機(jī)第7級(jí)轉(zhuǎn)子葉片為研究對(duì)象,采用精鍛成形工藝,對(duì)鍛造過(guò)程中出現(xiàn)的葉片腐蝕條帶組織進(jìn)行研究,揭示了腐蝕條帶的形成原因并提出了預(yù)防措施,以期為后續(xù)GH4169合金精鍛葉片的制造提供工程支撐。
1、試驗(yàn)
試驗(yàn)用原材料為直徑20mm的國(guó)產(chǎn)GH4169高溫合金棒材。壓氣機(jī)第7級(jí)轉(zhuǎn)子葉片經(jīng)過(guò)擠壓、鐓頭、預(yù)鍛和終鍛4步主要工序制備而成,主要成形方式如下:采用連續(xù)回轉(zhuǎn)爐對(duì)坯料加熱到1020~1060℃,保溫一段時(shí)間后,在400~1000t的電動(dòng)螺旋壓力機(jī)上成形。終鍛葉片在真空爐中進(jìn)行熱處理,經(jīng)固溶熱處理(950~965℃保溫1h)+時(shí)效熱處理(720℃保溫8h,爐冷至620℃保溫8h)后,采用Kalling試劑(100mLHCl+100mL酒精+50gCuCl2)進(jìn)行葉片鍛件表面腐蝕,發(fā)現(xiàn)葉片榫頭部位有如圖1a所示的
腐蝕條帶,條帶寬約1mm、長(zhǎng)約10mm,呈弧形,進(jìn)一步檢查發(fā)現(xiàn),該條帶部位呈現(xiàn)混晶組織,由拉長(zhǎng)晶粒和細(xì)小晶粒混合組成,平均晶粒度比葉根其他部位的晶粒度更細(xì),如圖1b—c所示。通過(guò)與葉片成品模型對(duì)比分析可知,該部位的腐蝕條帶無(wú)法通過(guò)后續(xù)機(jī)加工完全去除,殘留的條帶組織會(huì)造成葉片組織不合格,如圖1d所示。通過(guò)對(duì)葉片緣板轉(zhuǎn)接R處進(jìn)行顯微組織觀察發(fā)現(xiàn),沿輪廓外形的鍛造組織具有明顯的流線特征,該部位也呈現(xiàn)出拉長(zhǎng)晶粒和細(xì)小晶粒組成的混晶組織形貌,如圖1e—f所示,但轉(zhuǎn)接R處未形成明顯的條帶組織,且其高倍組織符合相關(guān)標(biāo)準(zhǔn)要求。
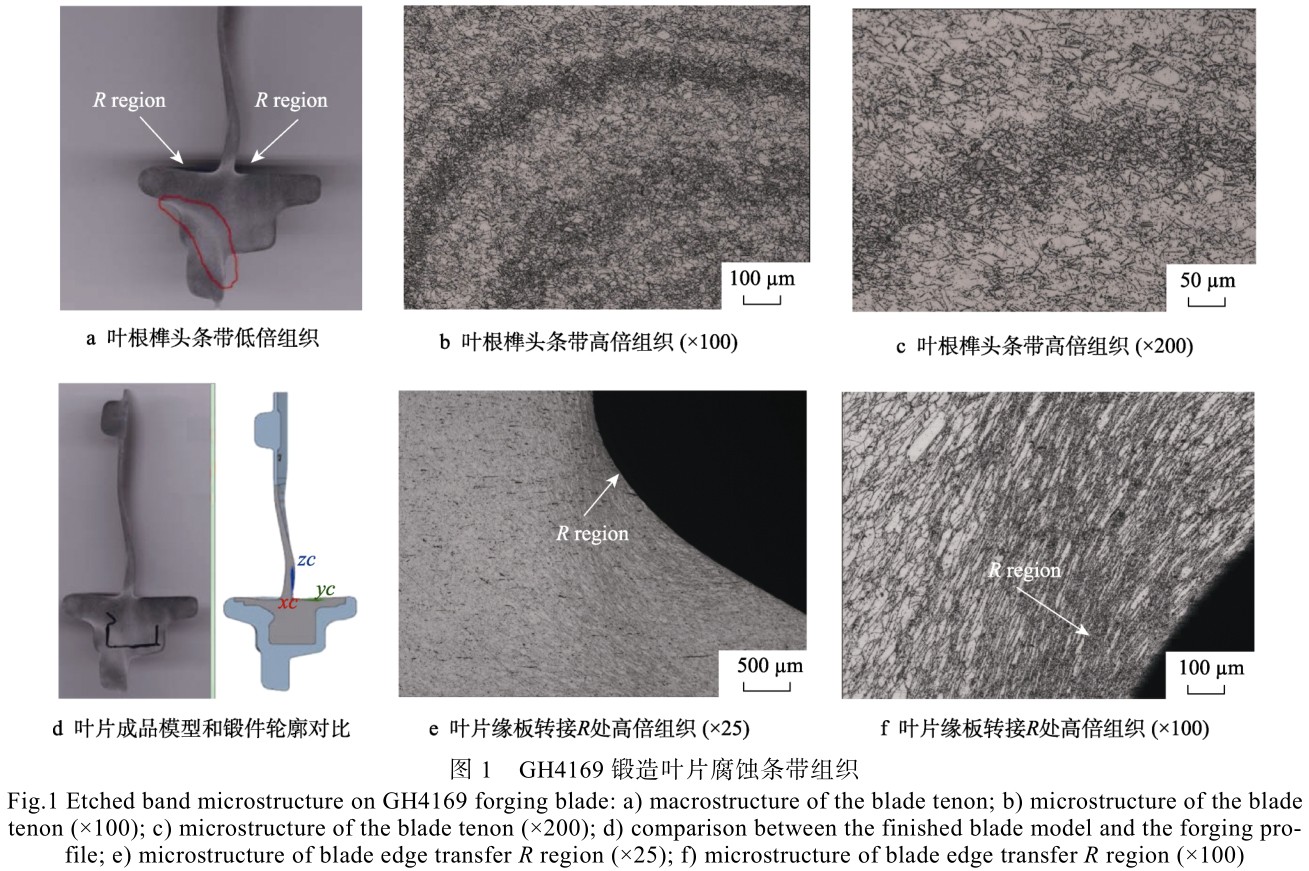
葉片榫頭處條帶組織由拉長(zhǎng)晶粒和細(xì)小再結(jié)晶晶粒組成,細(xì)小再結(jié)晶晶粒占比50%以上,再結(jié)晶晶粒尺寸通常因變形量大或變形溫度低而較小,而拉長(zhǎng)晶粒表明此處累積的變形量不足以完成全部再結(jié)晶,或者因變形溫度較低而難以實(shí)現(xiàn)完全再結(jié)晶。隨后隨機(jī)解剖了同批次多件葉片,均出現(xiàn)了類(lèi)似問(wèn)題,說(shuō)明該問(wèn)題的產(chǎn)生是批次性、通用性的,擬從原材料及鍛造工藝角度入手進(jìn)行原因排查分析。
2、結(jié)果與分析
2.1葉片鍛件用原材料
在前期某批次GH4169合金壓氣機(jī)轉(zhuǎn)子葉片精鍛過(guò)程中,進(jìn)行葉片縱向低倍檢查時(shí)發(fā)現(xiàn),葉根榫頭中心區(qū)域和葉身均有光亮線顯示,壓氣機(jī)轉(zhuǎn)子葉片縱向低倍條帶組織如圖2所示,壓氣機(jī)轉(zhuǎn)子葉片縱向高倍條帶組織如圖3所示,高倍組織顯示,亮條處存在析出相偏聚。對(duì)葉片榫頭條帶區(qū)域內(nèi)的析出相和基體在掃描電鏡下進(jìn)行能譜分析,結(jié)果如圖4和表1所示,據(jù)文獻(xiàn)[17]可知,δ相具有正交有序結(jié)構(gòu),其化學(xué)式為Ni3Nb,晶格常數(shù)a=0.3624nm、b=0.4251nm、c=0.7406nm,根據(jù)表1中析出相的成分可以判定析出相為δ相,即葉片析出相偏聚條帶為δ相條帶。
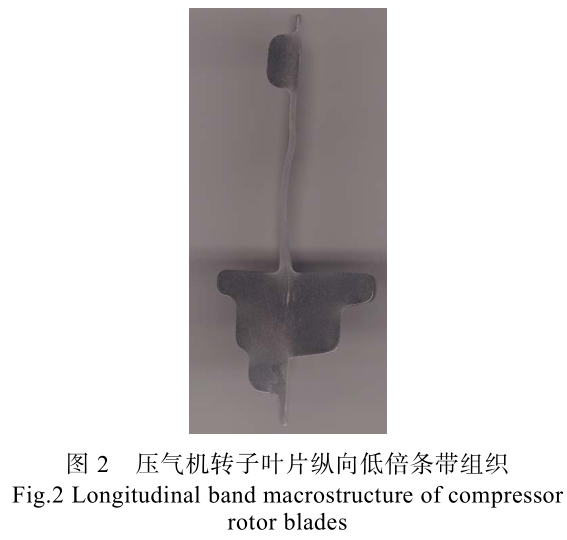
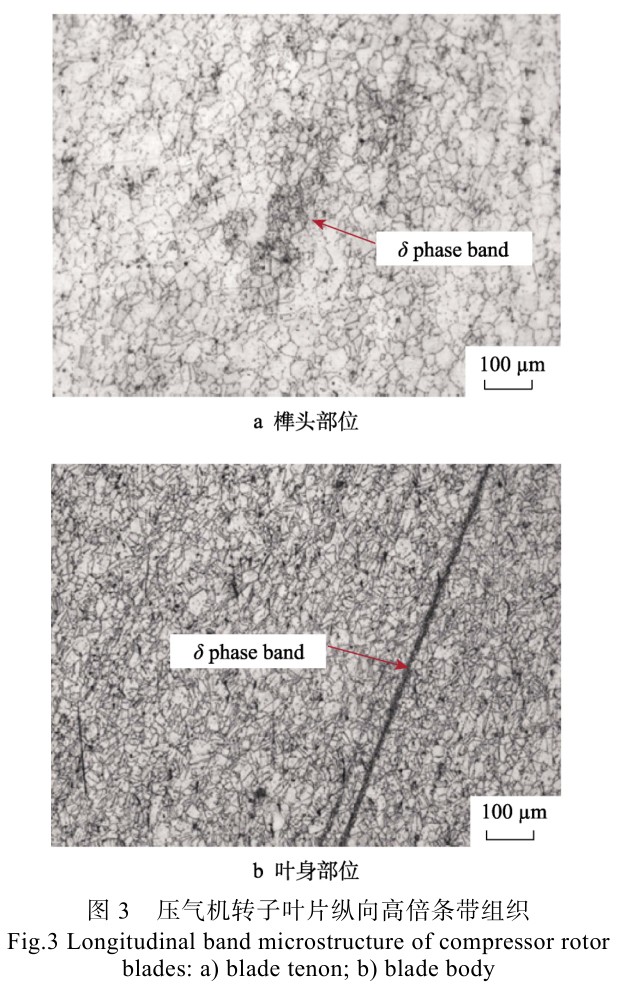
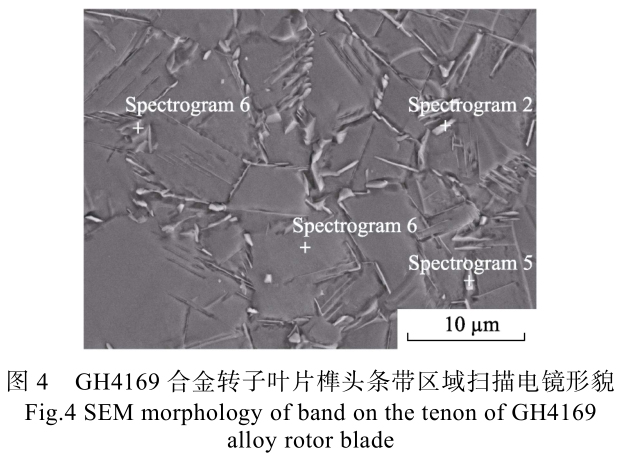

進(jìn)一步對(duì)鍛件用原材料開(kāi)展試驗(yàn)驗(yàn)證,選取原材料經(jīng)直接固溶+時(shí)效熱處理、1050℃保溫15min后再進(jìn)行固溶+時(shí)效熱處理,最后觀察金相組織(主要目的是讓原材料經(jīng)歷葉片鍛造的熱過(guò)程)。原材料經(jīng)直接固溶+時(shí)效熱處理后的晶粒組織為10級(jí)左右,整個(gè)截面分布有多條δ相條帶,如圖5所示。葉片鍛件用原材料經(jīng)1050℃保溫15min后再進(jìn)行固溶+時(shí)效熱處理,其顯微組織如圖6所示,可以看到,仍有輕微δ相條帶未完全溶解,晶粒組織在5.5級(jí)左右。
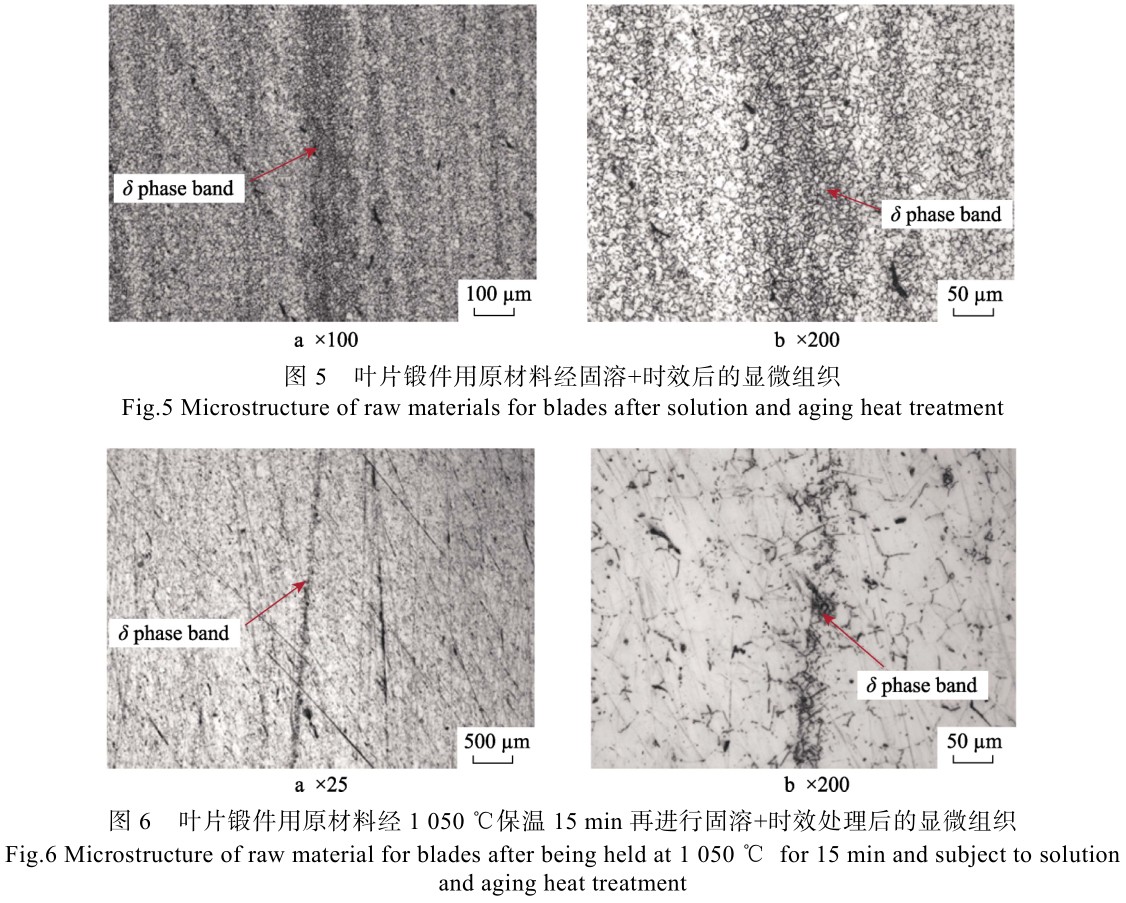
由上述試驗(yàn)可知,原材料中存在δ相偏聚是葉片鍛件出現(xiàn)條帶組織的一個(gè)原因,故在葉片鍛造之前需對(duì)原材料做好檢測(cè)驗(yàn)收,避免存在δ相偏聚的問(wèn)題。
第1章提到的壓氣機(jī)第7級(jí)轉(zhuǎn)子葉片鍛件用原材料經(jīng)固溶+時(shí)效處理后的顯微組織如圖7所示,未發(fā)現(xiàn)原材料存在δ相偏聚的異常現(xiàn)象,故此次產(chǎn)生腐蝕條帶的原因與原材料無(wú)關(guān)。
2.2葉片鍛造成形工藝分析
壓氣機(jī)第7級(jí)轉(zhuǎn)子葉片鍛件采用傳統(tǒng)的四火成形方案,即擠壓、鐓頭、預(yù)鍛、終鍛。經(jīng)復(fù)查,擠壓、鐓頭以及預(yù)鍛工序均采用前期鍛造葉片的通用制坯模,為了匹配成品葉片造型,對(duì)終鍛工序的模具進(jìn)行了特殊設(shè)計(jì)。但此批葉片根部造型與前期葉片造型存在較大差異,如圖8所示,葉根榫頭尺寸沿盆背、進(jìn)排氣側(cè)方向均有減小,而在實(shí)際生產(chǎn)時(shí)未考慮最終葉片造型的尺寸差異而采用了通用制坯模。通用制坯模和葉片成品造型不匹配,導(dǎo)致葉片終鍛時(shí)榫頭部位金屬余量較多,過(guò)多的金屬向后定位凸臺(tái)處流動(dòng),造成較大的應(yīng)變梯度,最終形成了低倍異常條帶組織。
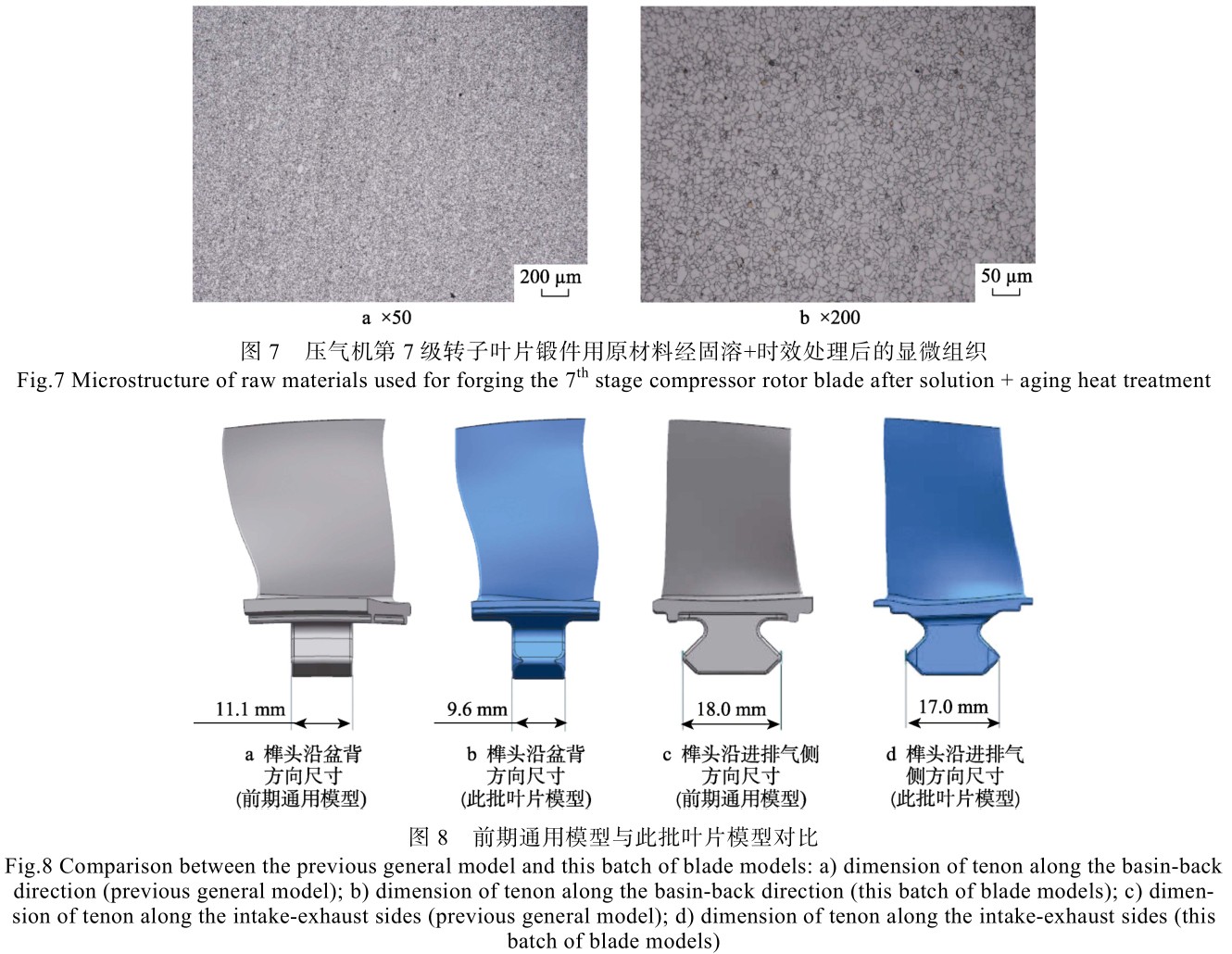
根據(jù)鍛造工藝進(jìn)一步開(kāi)展變形量計(jì)算,葉片為三維不對(duì)稱(chēng)形貌,如圖9所示,上下模分模面將葉根緣板及榫頭區(qū)域分為4部分,分別用1、2、3、4代表對(duì)應(yīng)的區(qū)域,分別用V1、V2、V3、V4代表每個(gè)區(qū)域的變形體積,用預(yù)鍛件和終鍛件相對(duì)應(yīng)的體積來(lái)表征變形量的大小。
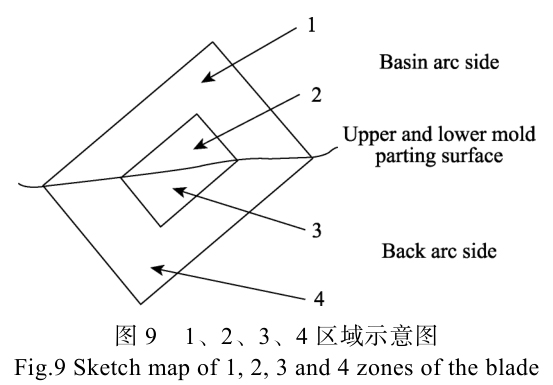
此批葉片鍛件采用通用制坯模和終鍛模2套模具,2套模具成形得出的葉根盆弧側(cè)與葉根背弧側(cè)的變形體積比分別為1.3和1.4,如式(1)所示。
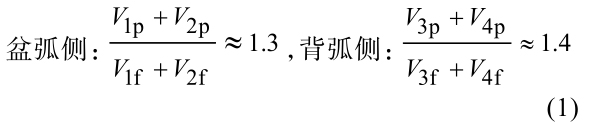
式中:V1p、V2p、V3p、V4p分別為預(yù)鍛件1—4區(qū)的變形體積;V1f、V2f、V3f、V4f分別為終鍛件1—4區(qū)的變形體積。
以上數(shù)據(jù)說(shuō)明,盆弧側(cè)與背弧側(cè)的總體金屬余量合適,變形量相對(duì)均勻,可滿(mǎn)足產(chǎn)品設(shè)計(jì)要求,但4個(gè)部分對(duì)應(yīng)的單獨(dú)變形體積比卻存在較大差異,尤其背弧側(cè)預(yù)鍛件與終鍛件的變形體積比最大約為1.8、最小卻為1.1,如式(2)所示。
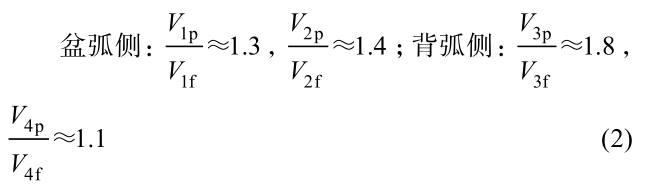
以上數(shù)據(jù)表明,盆弧側(cè)葉根緣板部分和葉根榫頭部分的金屬余量合適,金屬流動(dòng)正常,變形均勻,但背弧側(cè)葉根榫頭部分(3區(qū))金屬余量明顯偏大,變形量偏大,而葉根緣板部分4區(qū)的金屬余量偏小,變形量偏小,這樣會(huì)導(dǎo)致3區(qū)有過(guò)多的金屬流進(jìn)4區(qū),金屬跨區(qū)域異常流動(dòng),變形量分布不均勻并超出正常允許范圍。通過(guò)模鍛成形數(shù)值模擬發(fā)現(xiàn),榫頭部位變形不均勻,存在變形死區(qū),而部分區(qū)域的變形又較大,兩者之間存在應(yīng)變落差較大的區(qū)域,該區(qū)域與條帶組織存在高度的一致性,如圖10所示。鍛造過(guò)程的仿真和熱模擬技術(shù)可較好地選出合理的溫度場(chǎng)、等效應(yīng)力等工藝參數(shù),從而有效避免鍛造缺陷的產(chǎn)生[23]。
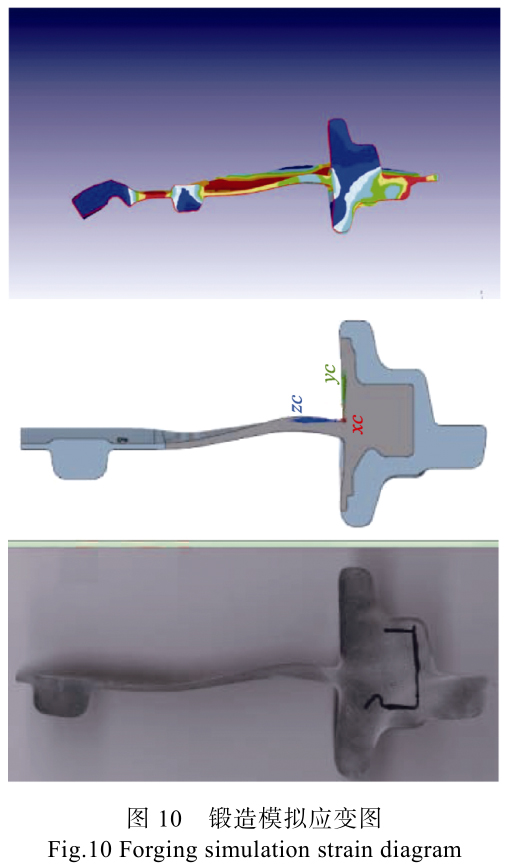
Chen等[24]對(duì)馬氏體不銹鋼渦輪葉片的鍛造過(guò)程進(jìn)行了仿真模擬,分析了變形、溫度、晶粒尺寸等的變化規(guī)律,得出了復(fù)雜鍛件的最佳熱鍛工藝。Kocanda等[25]分析了渦輪葉片熱鍛模擬成形規(guī)律,揭示了模具型腔定位及鍛造變形量對(duì)金屬流動(dòng)及模具側(cè)向力分布的影響。楊舜等[26]在葉片精鍛過(guò)程中采用數(shù)值模擬方法獲得了葉片從加壓到卸載整個(gè)過(guò)程的全部數(shù)值解,得出精鍛過(guò)程中任意時(shí)刻的溫度場(chǎng)、應(yīng)力–應(yīng)變分布、微觀組織演變規(guī)律及卸載后的殘余應(yīng)力和殘余應(yīng)變分布,還通過(guò)分析模具應(yīng)力分布、鍛造載荷及變形功等進(jìn)行了葉片模具模型設(shè)計(jì)和修正。因此,在制定葉片鍛造方案過(guò)程中采用數(shù)值模擬方法是確保產(chǎn)品合理成形的有效途徑。通過(guò)仿真模擬及成形分析,基本可確定此批葉片出現(xiàn)腐蝕條帶的主要原因?yàn)轭A(yù)鍛與終鍛變形量不匹配,進(jìn)而造成葉片榫頭局部應(yīng)變落差大而形成剪切帶。
2.3預(yù)防措施與驗(yàn)證
為了優(yōu)化鍛造工藝,結(jié)合葉片成品造型重新設(shè)計(jì)了一套預(yù)鍛模具,使預(yù)鍛件和終鍛件盆弧側(cè)、背弧側(cè)的變形體積比保持在1.3~1.4,盆弧側(cè)1、2區(qū)的變形體積比保持在1.1~1.2,背弧側(cè)3、4區(qū)的變形體積比保持在1.2~1.3,確保榫頭部位金屬余量適宜、變形均勻,如式(3)—(4)所示。
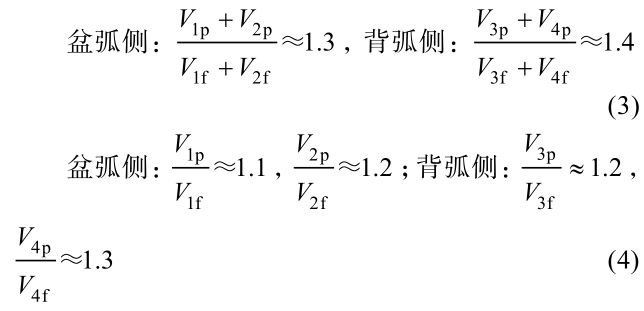
優(yōu)化預(yù)鍛模后再看葉根榫頭處的等效應(yīng)變,發(fā)現(xiàn)應(yīng)變條帶趨勢(shì)得到明顯改善,如圖11a所示。采用同爐批原材料進(jìn)行了一輪葉片鍛造工藝驗(yàn)證,葉片鍛件低倍組織得到明顯改善,葉根榫頭低倍腐蝕條帶消失,如圖11b所示,從而驗(yàn)證了形成腐蝕條帶組織是因?yàn)殄懺斐尚畏桨覆缓侠怼?/p>
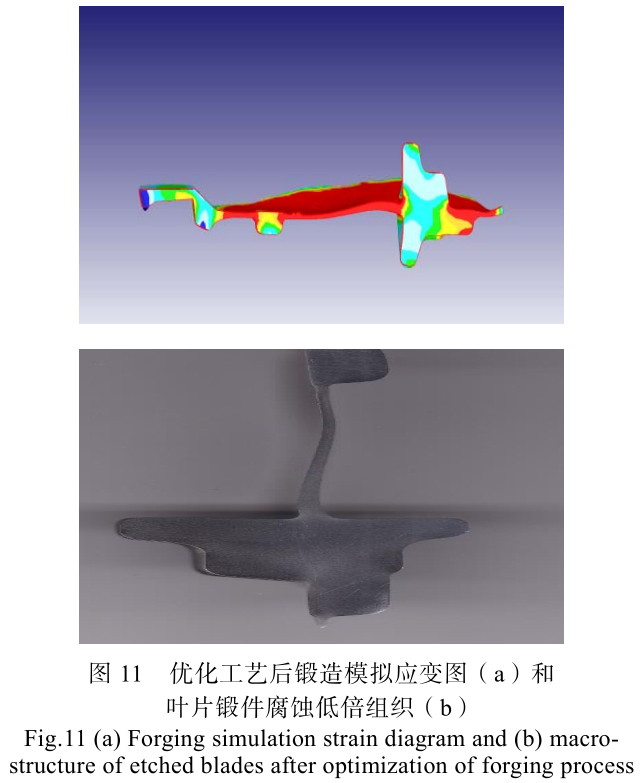
3、結(jié)論
1)原材料存在δ相偏聚是GH4169合金精鍛葉片存在腐蝕條帶的原因之一,在鍛造前需對(duì)原材料嚴(yán)格做好檢測(cè)驗(yàn)收。
2)鍛造成形工藝設(shè)計(jì)不合理將導(dǎo)致GH4169高溫合金精鍛葉片產(chǎn)生腐蝕條帶組織,在鍛造成形過(guò)程中應(yīng)確保葉片預(yù)鍛模和終鍛模變形相匹配,避免榫頭區(qū)域出現(xiàn)變形不均勻、產(chǎn)生應(yīng)變差。
3)結(jié)合數(shù)值模擬優(yōu)化鍛造工藝,使葉片預(yù)鍛件和終鍛件上下模具盆弧側(cè)、背弧側(cè)的變形體積比保持在1.1~1.4,這樣可使鍛造變形均勻、生產(chǎn)出低倍組織滿(mǎn)足要求的合格葉片。
4)在制定高溫合金葉片精鍛成形方案時(shí),應(yīng)采用數(shù)值模擬技術(shù)進(jìn)行工藝驗(yàn)證與優(yōu)化,以便準(zhǔn)確設(shè)定成形工藝參數(shù),確保葉片鍛件的組織和性能合格。
參考文獻(xiàn):
[1]張凱堯. 航空發(fā)動(dòng)機(jī)精鍛葉片銑削工裝結(jié)構(gòu)分析與優(yōu)化設(shè)計(jì)[D]. 煙臺(tái): 煙臺(tái)大學(xué), 2020: 10-14.
ZHANG Kai-yao. Structural Analysis and Optimal De-sign of Milling Fixture for Aeroengine Precision Forg-ing Blades[D]. Yantai: Yantai University, 2020: 10-14.
[2]高松, 李深亮. 航空發(fā)動(dòng)機(jī)精鍛葉片數(shù)字化數(shù)控加工技術(shù)[J]. 科技創(chuàng)新與應(yīng)用, 2019(10): 132-133.
GAO Song, LI Shen-liang. Digital Numerical Control Machining Technology for Precision Forged Blade of Aeroengine[J]. Technology Innovation Application,2019(10): 132-133.
[3]金辰懷. 應(yīng)用電感檢測(cè)技術(shù)評(píng)價(jià)精鍛葉片彎扭角[J].中國(guó)機(jī)械, 2022(7): 48-51.
JIN Chen-huai. The Inductance Detection Technique is Used to Evaluate the Bending and Twisting Angle of Precision Forged Blade[J]. Machine China, 2022(7):48-51.
[4]吳捍疆. 葉片精鍛成形過(guò)程的金屬流動(dòng)及殘余應(yīng)力研究[D]. 洛陽(yáng): 河南科技大學(xué), 2020: 13-14.
WU Han-jiang. Study on Metal Flow and Residual Stress in Blade Precision Forging[D]. Luoyang: Henan University of Science and Technology, 2020: 13-14.
[5]張凱堯, 孟慶恒, 馬瑞, 等. 影響航空發(fā)動(dòng)機(jī)精鍛葉片切削力的工藝分析[J]. 制造技術(shù)與機(jī)床, 2020(9): 35-39.
ZHANG Kai-yao, MENG Qing-heng, MA Rui, et al.Research on Crafts Analysis of Cutting Forces Affecting Marginless Precision Forging Blades[J]. Manufacturing Technology & Machine Tool, 2020(9): 35-39.
[6]楊根, 張立昌, 林何, 等. 航空葉片精鍛模具設(shè)計(jì)與數(shù)控加工[J]. 機(jī)床與液壓, 2020, 48(15): 109-113.
YANG Gen, ZHANG Li-chang, LIN He, et al. Design and NC Machining of Precision Forging Die of Aviation Blade[J]. Hydromechatronics Engineering, 2020, 48(15):109-113.
[7]袁飛, 呂彥明, 胡學(xué)超, 等. 汽輪機(jī)葉片精鍛模具預(yù)補(bǔ)償方法研究[J]. 現(xiàn)代制造工程, 2020(5): 113-118.
YUAN Fei, LYU Yan-ming, HU Xue-chao, et al. Re-search on Pre-compensation Method of Steam Turbine Blade Precision Forging Die[J]. Modern Manufacturing Engineering, 2020(5): 113-118.
[8]邵勇, 陸彬, 陳軍, 等. 精鍛葉片模具三維型面優(yōu)化技術(shù)[J]. 上海交通大學(xué)學(xué)報(bào), 2012, 46(10): 1616-1621.
SHAO Yong, LU Bin, CHEN Jun, et al. 3D Die Shape Optimization Technology for Net-Shape Forging of Aerofoil Blade[J]. Medical Bulletin of Shanghai Jiaotong University, 2012, 46(10): 1616-1621.
[9]鄢天燦. 航空葉片精鍛成形工藝分析及協(xié)同優(yōu)化方法研究[D]. 貴陽(yáng): 貴州大學(xué), 2021: 14-15.
YAN Tian-can. Process Analysis and Collaborative Op-timization of Precision Forging for Aircraft Blades[D].Guiyang: Guizhou University, 2021: 14-15.
[10] 關(guān)紅, 崔樹(shù)森, 汪大成. 高溫合金葉片精密成形技術(shù)研究[J]. 材料科學(xué)與工藝, 2013, 21(4): 143-148.
GUAN Hong, CUI Shu-sen, WANG Da-cheng. The Study of High Temperature Alloy Vane Precision Forming Technology[J]. Materials Science and Tech-nology, 2013, 21(4): 143-148.
[11] CHOUDHURY I A, EIBARADIE M A. Machinability of Nickel-base Super Alloys: a General Review[J].Journal of Materials Processing Technology, 1998,77(1/2/3): 278-284.
[12] 劉衛(wèi), 郝恒恒, 許安寧. GH4169 合金低倍暗色缺陷分析與研究[J]. 金屬加工(熱加工), 2022(5): 30-31.
LIU Wei, HAO Heng-heng, XU An-ning. Analysis and Study of Low Power Dark Color Defects of GH4169 alloy[J]. Metal Working, 2022(5): 30-31.
[13] 余江山. 高溫合金葉片精鍛成形研究[D]. 沈陽(yáng): 沈陽(yáng)理工大學(xué), 2008: 12-13.
YU Jiang-shan. Research on Precision Forging of Su-peralloy Blade[D]. Shenyang: Shenyang Ligong Uni-versity, 2008: 12-13.
[14] 齊歡. INCONEL 718(GH4169)高溫合金的發(fā)展與工藝[J]. 材料工程, 2012(8): 92-100.
QI Huan. Review of INCONEL 718 Alloy: Its History,Properties, Processing and Developing Substitutes[J].Journal of Materials Engineering, 2012(8): 92-100.
[15] 張利沖, 許文勇, 李周, 等. 鎳基高溫合金 GH4169 粉末表面氧化特性[J]. 航空材料學(xué)報(bào), 2020(40): 1-7.
ZHANG Li-chong, XU Wen-yong, LI Zhou, et al. Sur-face Oxidation Characteristics of Nickel-base Superal-loy GH4169 Powder[J]. Journal of Aeronautical Materi-als, 2020(40): 1-7.
[16] 王春光, 王東哲, 萬(wàn)紅, 等. 鍛造及熱處理工藝對(duì)GH4169 合 金 組 織 與 性 能 的 影 響 [J]. 鍛 壓 技 術(shù) ,2004(14): 16-18.
WANG Chun-guang, WANG Dong-zhe, WAN Hong, et al. Influence of Forging and Heat Treatment on Struc-ture and Property of GH4169 Alloy[J]. Forging &Stamping Technology, 2004(14): 16-18.
[17] 莊景云. 變形高溫合金 GH4169 鍛造工藝[M]. 北京:冶金工業(yè)出版社, 2006: 90-95.
ZHUANG Jing-yun. Forging Process of Deformed Su-peralloy GH4169[M]. Beijing: Metallurgical Industry Press, 2006: 90-95.
[18] 董建新. INCONEL718 高溫合金的發(fā)展[J]. 兵器材料科學(xué)與工程, 1996, 19(2): 46-50.
DONG Jian-xin. Development of INCONEL 718 Super-alloy[J]. Ordnance Material Science and Engineering,1996, 19(2): 46-50.
[19] COZAR R, PINEAU A. Morphology of γ ′and γ″ Pre-cipitates and Thermal Stability of Inconel 718 Type Al-loys[J]. Metallurgical Transactions, 1973, 4(1): 47-59.
[20] 謝錫善, 董建新, 付書(shū)紅, 等. γ″和 γ′相強(qiáng)化的 Ni-Fe基高溫合金 GH4169 的研究與發(fā)展[J]. 金屬學(xué)報(bào),2010, 46(11): 1289-1302.
XIE Xi-shan, DONG Jian-xin, FU Shu-hong, et al. Re-search and Development of γ″ and γ′ Strengthened Ni-Fe Base Superalloy GH4169[J]. Acta Metallurgica Sinica, 2010, 46(11): 1289-1302.
[21] 詹梅, 劉郁麗, 楊合. 航空葉片的精鍛工藝與模擬技術(shù)[J]. 重型機(jī)械, 1999(6): 1-3.
ZHAN Mei, LIU Yu-li, YANG He. Precise Forging Process and Simulation Technology for Aeronautical Blade[J]. Heavy Machinery, 1999(6): 1-3.
[22] 鐘杰, 胡楚江, 郭成. 葉片精密鍛造技術(shù)的發(fā)展現(xiàn)狀及其展望[J]. 鍛壓技術(shù), 2008, 33(1): 1-5.
ZHONG Jie, HU Chu-jiang, GUO Cheng. Development Status and Prospects of Blade Precision Forging Tech-nology[J]. Forging & Stamping Technology, 2008,33(1): 1-5.
[23] 李娜, 尹喜剛, 劉靜, 等. 鍛造仿真與熱模擬技術(shù)在航空發(fā)動(dòng)機(jī)葉片精密鍛造中的應(yīng)用[J]. 航空制造技術(shù),2018, 61(15): 59-62.
LI Na, YIN Xi-gang, LIU Jing, et al. Application of Forging Simulation and Thermal Simulation Technology in Precision Forging of Aero-Engine Blade[J]. Aeronau-tical Manufacturing Technology, 2018, 61(15): 59-62.
[24] CHEN F, REN F, CHEN J, et al. Microstructural Mod-eling and Numerical Simulation of Multi-physical Fields for Martensitic Stainless Steel during Hot Forging
Process of Turbine Blade[J]. The International Journal of Advanced Manufacturing Technology, 2016, 82(1):85-98.
[25] KOCANDA A, CZYZEWSKI P, MEHDI K H. Nu-merical Analysis of Lateral Forces in a Die for Turbine Blade Forging[J]. Archives of Civil & Mechanical En-gineering, 2009, 9(4): 49-54.
[26] 楊舜, 李宏, 劉印剛, 等. 葉片精密鍛造過(guò)程數(shù)值模擬技術(shù)研究進(jìn)展[J]. 精密成形工程, 2015, 7(6): 44-51.
YANG Shun, LI Hong, LIU Yin-gang, et al. A Review on the Numerical Simulation Technology of Aerofoil Blade Precision Forging Process[J]. Journal of Netshape Forming Engineering, 2015, 7(6): 44-51.
相關(guān)鏈接